Floors and Foundations
There is an old saying that the main thing every building needs is a good set of boots and a good hat. The boots are there to provide strong and waterproof foundations, the hat is there to provide protection from the rain and sun.
Cement has revolutionised building construction over the last century both in the construction of multi-storey buildings and in the production of durable and waterproof foundations. However, the cement industry is responsible for 8% of global anthropogenic CO2 emissions, making it the third biggest contributor to global warming after energy production and transportation industries. Developed economies are consequently looking for ways to reduce the cement content of buildings and find low carbon solutions to building construction. Foundations are the area where it is most difficult to devise substitutes, but engineering to minimise the volume of concrete is a good starting point.
Stone
In the days before cement, stone provided the traditional foundations for a building. If local stone is available it is generally the most sustainable option.
A foundation for a single storey building is usually created by cutting a trench through existing ground to a depth of 600-900mm and around 450-600mm wide. Filling this with stone reinforces the ground underneath external walls and reduces the possibility of subsidence. Rocks can be used without cutting or 'dressing' providing that smaller stones are used in between to provide a stable base layer. Generally the layer of stones is then capped by a ring beam of reinforced concrete to provide a level base as a datum for the floor slab and external walls.

AWF Primaries The schools are built on traditional rubble stone foundations - without the use of concrete
Case Studies:
Concrete
Use concrete and cement sparingly. Cement is expensive and its manufacture is one of the primary causes of global warming.
Concrete is composed of cement, sand and aggregate in a typical ratio of 1:2:4. it is the strongest material to use for both foundations and ground floor slabs and good quality concrete has waterproofing capabilities - though this can be improved by incorporating a plastic sheet as a damp-proof membrane. Unfortunately, cement is an imported material which is both expensive and unecological, producing substantial quantities of carbon dioxide in its manufacture. Efforts should be made to limit the use of concrete wherever possible and use cement sparingly.


Lake Bunyonyi Secondary Bricks are inlayed into the first floor formwork to reduce the amount of concrete required.
Case Studies:
Limecrete
Concerns over the industry's increasing carbon emissions have led to a resurgence of lime as an alternative binding agent to cement.
Although cement has been the conventional binder since the 20th century, lime was the traditional binder for centuries before that. Lime is not as strong as cement, nor does it have the same waterproofing qualities. However, this can be an advantage as lime is hydroscopic giving it the ability to effectively regulate temperature and humidity. Lime requires less energy in its production than cement and sequesters carbons as it hardens. The recommended mix is 1:3 of lime to sand and aggregate mixture. Limecrete can be used to create floor slabs and consolidate a stone foundation to provide the footing for walls and frames.

The Pantheon Temple in Rome has a limecrete dome spanning over 43m that has survived nearly 2000 years
Earth
Earthen floor technology has progressed significantly from unsanitary dirt flooring and now represents a cost effective and durable alternative to concrete.
Consolidated earthen floors simply use the material excavated from site as a result of digging foundations. However, unlike traditional dirt flooring, cement-free earthen flooring is durable, waterproof and washable. The earthen floor system, which has been developed by Earth Enable, is made from different layers of compressed natural material sealed with linen oil, which permeates the fine earthen mix and forms a waterproof and plastic-like resin on top. Earth Enable predicts that in the East African climate earthen floors should last 10-15 years if maintained with a fresh coat of oil every 3 years.
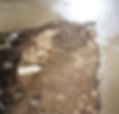
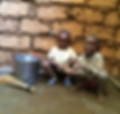
RLS Dormitory ASA collaborated with Earth Enable to produce cement-free sustainable earthen flooring.
Case Studies:
Tiles
Concrete, ceramic or clay tiles and bricks can provide a durable and decorative floor surface.
A ceramic tiled floor on a concrete slab provides a very durable, though expensive, floor finish. Production of ceramic floor tiles is carbon intensive due to cement content and the energy required for firing. A fired brick or concrete tile floor laid in cement or lime mortar will be less costly and more sustainable but more difficult to keep clean. Compressed earthen floor tiles, stabilised with a little cement or lime are more sustainable but still remain an uncommon and relatively undeveloped technology.


Ruhehe Primary The cement floor tiles contain volcanic stone dust as aggregate to reduce costly sand and gravel content.
Case Studies: